核心提示:從蒸汽機(jī)時(shí)代到電氣化時(shí)代,從電氣化時(shí)代到信息時(shí)代,背后制造工廠有了顯著變化。從早期的英國(guó)、德國(guó)手工打造蒸汽機(jī),到風(fēng)靡一
從蒸汽機(jī)時(shí)代到電氣化時(shí)代,從電氣化時(shí)代到信息時(shí)代,背后制造工廠有了顯著變化。從早期的英國(guó)、德國(guó)手工打造蒸汽機(jī),到風(fēng)靡一時(shí)的福特流水生產(chǎn)線,再到大規(guī)模集成、自動(dòng)化手臂投入使用,每一個(gè)時(shí)代都有與其特點(diǎn)相對(duì)應(yīng)的制造工廠。
如今,隨著從信息時(shí)代向智能時(shí)代進(jìn)發(fā),全球制造業(yè)正在經(jīng)歷工業(yè)4.0變革。大量工廠要接受數(shù)字化轉(zhuǎn)型的洗禮,追求智能工廠的精益求精、人力解放、生產(chǎn)效率大幅提高。
11月4日,馬斯克現(xiàn)身2022年度巴倫投資大會(huì),提到一個(gè)工廠小事。他在生產(chǎn)線發(fā)現(xiàn)電池組頂部有三個(gè)玻璃纖維墊,問(wèn)有什么用處?靜音團(tuán)隊(duì)以為那是安全團(tuán)隊(duì)要的,用來(lái)防止火災(zāi);安全團(tuán)隊(duì)以為是靜音團(tuán)隊(duì)要的,用來(lái)降噪。這個(gè)烏龍導(dǎo)致生產(chǎn)線阻塞,馬斯克明白后立馬去掉了玻璃纖維墊。
特斯拉超級(jí)工廠無(wú)疑是當(dāng)今智能工廠的代表。這一細(xì)節(jié)表明,無(wú)論工廠自動(dòng)化、智能化程度多么高,具有自主判斷能力的人,仍然不可或缺。
中國(guó)近幾十年來(lái),有“世界工廠”之稱(chēng),在向智能制造進(jìn)化的途中,如何實(shí)現(xiàn)工廠、機(jī)器、人工智能與人的有機(jī)協(xié)作,共同進(jìn)化,或許是擺在中國(guó)智能制造面前必須要克服的課題。
而這同時(shí)也蘊(yùn)含著刷新中國(guó)智能制造的新內(nèi)涵。
告別狂野增長(zhǎng)
對(duì)于這一問(wèn)題的理解,可以以大規(guī)模手機(jī)生產(chǎn)為例。以前功能機(jī)本身不智能,2007年才開(kāi)始智能,在這之后的10年,智能手機(jī)行業(yè)野蠻生長(zhǎng),機(jī)遇多于挑戰(zhàn)。
作為傳統(tǒng)國(guó)產(chǎn)品牌,OPPO擁有自己的工廠,公開(kāi)資料顯示,與業(yè)內(nèi)其它手機(jī)廠商不同,其手機(jī)自產(chǎn)率超過(guò)80%。
據(jù)OPPO制造與品質(zhì)事業(yè)部總裁郭小聰回憶,OPPO 2008年時(shí)一個(gè)月只能生產(chǎn)20萬(wàn)臺(tái)手機(jī),到2016年增至200萬(wàn)臺(tái)/月,2019年更達(dá)到了2000萬(wàn)臺(tái)/月,十年內(nèi)產(chǎn)能增大了100倍。
這一過(guò)程中,OPPO既要擴(kuò)大自有制造的產(chǎn)能,又要實(shí)現(xiàn)數(shù)字化轉(zhuǎn)型,讓工廠更智能。
然而 ,2017年,全球智能手機(jī)出貨量沖上巔峰,行業(yè)進(jìn)入飽和期,上下游發(fā)生了變化。一方面,消費(fèi)者需求日益精細(xì)化,導(dǎo)致手機(jī)SKU增加;另一方面,廠商的產(chǎn)品品類(lèi)橫向增長(zhǎng),擴(kuò)展至智能手表等IoT產(chǎn)品。OPPO以往一年只生產(chǎn)10-20款產(chǎn)品,現(xiàn)在一年已增至60-80款產(chǎn)品。各方的變化對(duì)制造水平提出了更高的要求。
手機(jī)作為消費(fèi)電子產(chǎn)品頭號(hào)品類(lèi),制造卻不如白電行業(yè)成熟。其特點(diǎn)是市場(chǎng)變化快、產(chǎn)品周期短。需求改變導(dǎo)致生產(chǎn)變化,生產(chǎn)變化意味著產(chǎn)能發(fā)生改變,而產(chǎn)能又會(huì)影響到物流倉(cāng)儲(chǔ);產(chǎn)品生產(chǎn)從定義、測(cè)試到組裝等環(huán)節(jié),標(biāo)準(zhǔn)都不同,例如折疊屏和直板手機(jī)工藝不同,所需要的螺絲標(biāo)準(zhǔn)也不一樣。整個(gè)鏈條若沒(méi)有統(tǒng)一標(biāo)準(zhǔn)管理,將產(chǎn)生大量的資源浪費(fèi),成本增倍。
上世紀(jì)初,福特汽車(chē)用流水線生產(chǎn)模式打開(kāi)了汽車(chē)工業(yè)革命的大門(mén)。這家公司通過(guò)減少SKU,擴(kuò)大規(guī);(yīng),以降低成本,交付更多汽車(chē),讓消費(fèi)者用更低的價(jià)格買(mǎi)到產(chǎn)品。
時(shí)過(guò)境遷,單純調(diào)整生產(chǎn)線已經(jīng)無(wú)法滿足當(dāng)前市場(chǎng)需求,智能化轉(zhuǎn)型才是最優(yōu)解。
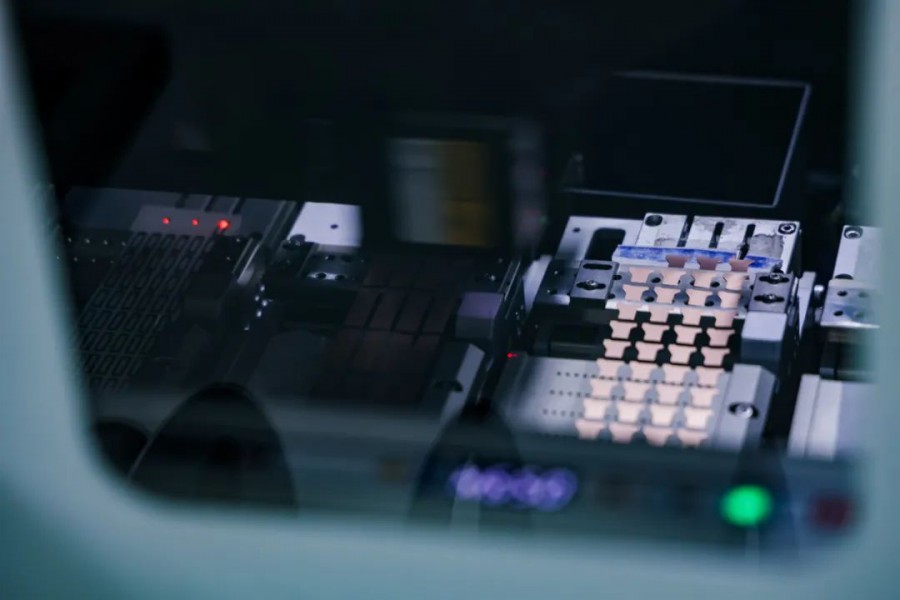
OPPO在實(shí)踐中意識(shí)到智能化轉(zhuǎn)型的重要性。2017年,OPPO全球化布局走向歐洲運(yùn)營(yíng)商市場(chǎng),發(fā)現(xiàn)這里的玩法與傳統(tǒng)運(yùn)作模式發(fā)生了沖突:歐洲運(yùn)營(yíng)商會(huì)先給你13周的訂單,但傳統(tǒng)的玩法是先主觀預(yù)測(cè)產(chǎn)量。面對(duì)這一情況,OPPO一時(shí)有些措手不及。
加之市場(chǎng)飽和期,疫情以及國(guó)際經(jīng)濟(jì)形勢(shì)等方面的影響,都證明了原先預(yù)測(cè)訂單生產(chǎn)模式已不適應(yīng)當(dāng)下市場(chǎng)環(huán)境。
調(diào)整已成必然。通過(guò)一系列內(nèi)外疏通,從標(biāo)準(zhǔn)化、自動(dòng)化、數(shù)字化,到智能化,3年時(shí)間,OPPO郭小聰表示,把制造周期從16天調(diào)整到6.8天,最新推出的Reno9即是如此。
他表示,從2023年起,將從預(yù)測(cè)生產(chǎn)模式轉(zhuǎn)為ATO(按訂單式)模式,即不再采用主觀決策,而是先獲取代理商需求,規(guī)范其對(duì)自身訂單的預(yù)估,從而縮短后續(xù)制造流程的時(shí)間。從準(zhǔn)備原料、組裝貼片,到總裝、測(cè)試,再到物流,制造周期進(jìn)一步縮短至6天以下。
機(jī)械臂不等于智能制造
沒(méi)有統(tǒng)一標(biāo)準(zhǔn)前,一切“智能”都是紙老虎。
從2016年到2020年,OPPO內(nèi)部引入了大量的自動(dòng)化設(shè)備,而這些設(shè)備的導(dǎo)入時(shí)間前后差異導(dǎo)致設(shè)備設(shè)計(jì)差異比較大。想要讓所有的設(shè)備保持生產(chǎn)一致性,首先第一步要做的就是標(biāo)準(zhǔn)化。
據(jù)郭小聰透露,公司在2020-2022年期間基本按下了擴(kuò)張“暫停鍵”,不再大量引進(jìn)新設(shè)備,為的是重新梳理工廠里標(biāo)準(zhǔn)化流程。
OPPO 做了三件事情:
第一,物理標(biāo)準(zhǔn)化。彼時(shí)OPPO有15000臺(tái)設(shè)備,要把同功能的不同設(shè)備歸類(lèi),把不同供應(yīng)商設(shè)備歸類(lèi);
第二,數(shù)字標(biāo)準(zhǔn)化。由于不同供應(yīng)商設(shè)備之間的系統(tǒng)完全不同,OPPO花了大量精力搭建新的軟件控制平臺(tái),從而實(shí)現(xiàn)一個(gè)軟件管理不同供應(yīng)商的硬件設(shè)備;
第三,海外建廠標(biāo)準(zhǔn)化。由于國(guó)內(nèi)外的法律法規(guī)等因素,廠房落地的情況不同,OPPO將海外建廠的流程標(biāo)準(zhǔn)化,可實(shí)現(xiàn)全球各地應(yīng)要求快速建廠。
原先中國(guó)企業(yè)數(shù)字化最為人詬病的,就是沒(méi)有自己的軟件系統(tǒng),硬件買(mǎi)回來(lái)能裝,卻需要供應(yīng)商來(lái)管理,這大大影響了生產(chǎn)效率和設(shè)備維護(hù)成本。
不僅是硬件設(shè)備的軟件不同,財(cái)務(wù)和研發(fā)管理等系統(tǒng)軟件也不同。各系統(tǒng)之間的割裂導(dǎo)致信息不流通,這也是傳統(tǒng)企業(yè)數(shù)字化時(shí)頭疼的問(wèn)題。例如ERP(企業(yè)資源管理)、CRM(全單銷(xiāo)售管理)和TMS(物流運(yùn)輸管理系統(tǒng))之間無(wú)法無(wú)縫交換信息,從上至下的影響,致使管理過(guò)程不透明。
據(jù)郭小聰舉例說(shuō),公司以前與供應(yīng)商的溝通方式比較傳統(tǒng),生產(chǎn)計(jì)劃鏈條一致性很差。外部的訂單需求是一個(gè)計(jì)劃,來(lái)到集成產(chǎn)品交付部,得消化分解成物料需求計(jì)劃和生產(chǎn)執(zhí)行計(jì)劃,供應(yīng)鏈接到的又是新計(jì)劃。一個(gè)鏈條里計(jì)劃混亂,信息無(wú)法打通,溝通成本高。
于是OPPO在2020年啟動(dòng)了供應(yīng)鏈系統(tǒng)變革,以解決內(nèi)部計(jì)劃和外部供應(yīng)商計(jì)劃不一致,完成供應(yīng)鏈管理系統(tǒng)(SRM)升級(jí),打通了跟供應(yīng)商的交付信息鏈路。
到2021年將全公司切換至全新協(xié)同辦公平臺(tái)TT和公司應(yīng)用協(xié)同辦公平臺(tái)MO,把 ERP、PLM、研發(fā)管理和財(cái)務(wù)管理等系統(tǒng)要素集成,用一個(gè)系統(tǒng)串聯(lián)起不同的環(huán)節(jié),讓信息流在同一個(gè)平臺(tái)上跑了起來(lái)。
這些所有前置性的標(biāo)準(zhǔn)定下之后,才算搭建好智能制造基礎(chǔ)。
數(shù)字化轉(zhuǎn)型轉(zhuǎn)到哪里
標(biāo)準(zhǔn)化之后,切實(shí)的自動(dòng)化才能進(jìn)一步實(shí)現(xiàn)“智能”。
Counterpoint Research的數(shù)據(jù)顯示,2021年,中國(guó)貢獻(xiàn)了全球67%的手機(jī)產(chǎn)量,全球每3臺(tái)手機(jī),有2部是中國(guó)造。盡管中國(guó)是全球公認(rèn)的世界工廠,但全球建廠可以降低成本,這又帶來(lái)了新的挑戰(zhàn)。
OPPO全球擁有10個(gè)智能制造中心,包括印度、巴基斯坦和埃及等海外工廠。怎么讓這些工廠標(biāo)準(zhǔn)統(tǒng)一?
首先,在生產(chǎn)環(huán)節(jié)中,OPPO使用了一些技術(shù)手段,實(shí)現(xiàn)了各工廠要求的標(biāo)準(zhǔn)化,通過(guò)(AOI:Auto Optical Inspection)光學(xué)檢測(cè)系統(tǒng)的導(dǎo)入,把對(duì)關(guān)鍵工藝的外觀標(biāo)準(zhǔn)進(jìn)行了量化固化。如在貼片工序之后的印刷流程,通過(guò)全球統(tǒng)一的視覺(jué)檢測(cè)設(shè)備導(dǎo)入,保證了全球各工廠工藝參數(shù)和管控要求的一致,以保證印刷質(zhì)量。
這一環(huán)節(jié)不僅在技術(shù)上代替了肉眼判斷,更精確,且通過(guò)數(shù)字化將判定標(biāo)準(zhǔn)上傳至系統(tǒng),再應(yīng)用到全球其它工廠,可保證各工廠的交付一致性。
其次,OPPO還嘗試了VR方案。如折疊屏手機(jī)的生產(chǎn)涉及新設(shè)備操作與工藝要求,當(dāng)印度工廠需設(shè)備調(diào)試時(shí),工程師就得出國(guó)。OPPO選擇與工業(yè)VR公司合作,通過(guò)遠(yuǎn)程設(shè)備進(jìn)行指導(dǎo)校準(zhǔn),以擺脫國(guó)際人員來(lái)往的束縛。
OPPO不僅自產(chǎn)率超過(guò)80%,還有擁有極強(qiáng)的產(chǎn)業(yè)協(xié)同能力。在數(shù)字化轉(zhuǎn)型過(guò)程中,該能力的優(yōu)勢(shì)被放大。
通過(guò)制造與研發(fā)相互磨合,OPPO優(yōu)化了制造工藝,實(shí)現(xiàn)量產(chǎn)的易制造性、可制造性和可靠性。旗艦產(chǎn)品往往會(huì)使用新材料、新工藝和新設(shè)備,初期生產(chǎn)良率低。通過(guò)產(chǎn)研協(xié)同,設(shè)計(jì)研發(fā)階段就可提前為后續(xù)生產(chǎn)和制造預(yù)留合理公差,避免來(lái)回返工。
郭小聰舉了個(gè)例子,折疊屏講究縫隙控制得好,并保證設(shè)計(jì)方案能讓供應(yīng)商生產(chǎn)出來(lái)。工業(yè)領(lǐng)域,每個(gè)零部件尺寸都在0.01mm上下波動(dòng),而多個(gè)部件疊加會(huì)影響最終的縫隙。在產(chǎn)研協(xié)同幫助下,OPPO折疊屏生產(chǎn)良率行業(yè)居前。
2017年至今,OPPO在設(shè)備領(lǐng)域投入,除了產(chǎn)能擴(kuò)張的設(shè)備,剩下50~60%的設(shè)備投入都用于品質(zhì)提升與標(biāo)準(zhǔn)化、數(shù)字化和智能化升級(jí),總投入接近20億元人民幣。
2020年,OPPO啟動(dòng)了“鳳凰計(jì)劃”,實(shí)現(xiàn)全面數(shù)字化轉(zhuǎn)型。
人性化底色,讓00后參與智能化
在中國(guó)人口眾多、中老年人慢慢增多的人口結(jié)構(gòu)下,拋開(kāi)“人”談數(shù)字化、智能化轉(zhuǎn)型,不切實(shí)際。
此前OPPO重慶工廠里有一個(gè)崗位離職率非常高,每個(gè)月該崗位平均換掉兩個(gè)人。公司做了一個(gè)調(diào)研報(bào)告,發(fā)現(xiàn)“最不愿意干的崗位”排名第一的永遠(yuǎn)是那個(gè)崗位。
調(diào)查發(fā)現(xiàn),原來(lái)該崗位工作強(qiáng)度很強(qiáng),要用手去扣電池蓋。在設(shè)計(jì)中,卡扣越多越牢固,但卡扣越多,員工的手越難受。OPPO發(fā)現(xiàn)問(wèn)題后,馬上找工程師做了一套自動(dòng)化設(shè)備,員工只需做一個(gè)預(yù)扣的動(dòng)作,剩下的裝配步驟便可交給設(shè)備。
如此一來(lái),員工工作強(qiáng)度變小了,該崗位的離職率大大降低。配套措施調(diào)整后,重慶工廠的離職率也從原先15%降低到了2%。
“工人很多反對(duì)自動(dòng)化、智能化,因?yàn)檫@是革他們的工作飯碗。”郭小聰說(shuō)。他對(duì)于數(shù)字化、智能化的定義,是希望未來(lái)所有的工人都能通過(guò)簡(jiǎn)單、低代碼方案提升自己工作效率。
以人為本,是OPPO數(shù)字化轉(zhuǎn)型核心。OPPO的POU手邊化(衡量工人不用挪動(dòng)身體作業(yè)的一個(gè)指標(biāo))達(dá)到了90%,員工不需要轉(zhuǎn)身、彎腰和走動(dòng),就能完成他觸手可及半徑內(nèi)的所有作業(yè)。OPPO還推出了五星人才激勵(lì)計(jì)劃,建立員工晉升通道,可從技能成長(zhǎng)到薪酬福利等方面得到支持。
越來(lái)越多的00后進(jìn)工廠,相比之下,他們更加厭倦傳統(tǒng)的機(jī)械化工作方式。但隨著智能化轉(zhuǎn)型深入,困擾著00后進(jìn)廠的問(wèn)題正在得到解決。
智能化轉(zhuǎn)型的本質(zhì)是為了追求生產(chǎn)效率,而“人”應(yīng)當(dāng)隨著轉(zhuǎn)型升級(jí),由原先的基礎(chǔ)工作升級(jí)為更高質(zhì)量的工作,從而提高員工的產(chǎn)出。郭小聰認(rèn)為智能制造不是自上而下的管理,而是從上面推動(dòng),下面能加入,大家共同達(dá)成全員數(shù)字化、智能化目標(biāo)。
尾聲
全球競(jìng)爭(zhēng)中,中國(guó)制造正在經(jīng)受挑戰(zhàn)。對(duì)于未來(lái)的競(jìng)爭(zhēng),主流意見(jiàn)已經(jīng)明確,發(fā)展實(shí)體經(jīng)濟(jì),走高質(zhì)量路線。
從拼價(jià)格,到拼品質(zhì),中國(guó)智能制造轉(zhuǎn)型升級(jí),最核心變量,依然是人。
早在2013年,德國(guó)就提出工業(yè)4.0的概念,美國(guó)也正在重新憧憬實(shí)體制造榮光。中國(guó)擁有全球最大的一塊工業(yè)沃土,產(chǎn)業(yè)鏈?zhǔn)滞暾,從上游材料再到下游組裝,這里可以形成一個(gè)完整的手機(jī)產(chǎn)業(yè)鏈閉環(huán),還擁有強(qiáng)大的工業(yè)技術(shù)保障和人才體系保障。在現(xiàn)有優(yōu)勢(shì)上,如何讓人與智能產(chǎn)線和諧相處,共同進(jìn)化,才是未來(lái)中國(guó)實(shí)體經(jīng)濟(jì)制勝之道。
OPPO是業(yè)內(nèi)少有的產(chǎn)研一體科技企業(yè),但目前OPPO已取得了一些階段性成果:SMT自動(dòng)化生產(chǎn)達(dá)到85%,自動(dòng)化測(cè)試達(dá)到90%,SMT 全自動(dòng)生產(chǎn)線和總裝生產(chǎn)效率都處于行業(yè)領(lǐng)先。每條生產(chǎn)線平均每10秒生產(chǎn)一臺(tái)手機(jī),對(duì)比2020年,一臺(tái)機(jī)器制造成本下降接近40%。
智能化轉(zhuǎn)型這條路,播下的是一顆待收獲的種子。
這讓人想到當(dāng)年OPPO堅(jiān)持自身特色的篤定。2012年,互聯(lián)網(wǎng)手機(jī)爆火,外界紛紛認(rèn)為線下渠道會(huì)被電商攻破時(shí),OPPO依舊堅(jiān)持經(jīng)營(yíng)線下渠道精細(xì)化、人性化轉(zhuǎn)型、深耕,終于在2016年爆發(fā),明星機(jī)型R9售出2000萬(wàn)臺(tái),成為安卓機(jī)單品銷(xiāo)量冠軍。
假以時(shí)日,OPPO堅(jiān)持的人性化底色的智能進(jìn)化,或許能成為中國(guó)智能制造轉(zhuǎn)型升級(jí)道路上一道風(fēng)景。
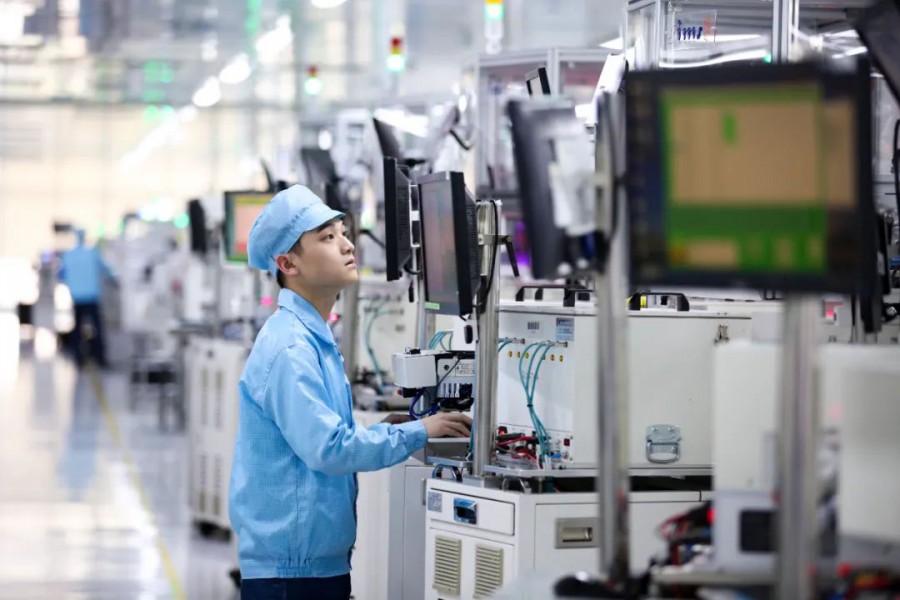
如今,隨著從信息時(shí)代向智能時(shí)代進(jìn)發(fā),全球制造業(yè)正在經(jīng)歷工業(yè)4.0變革。大量工廠要接受數(shù)字化轉(zhuǎn)型的洗禮,追求智能工廠的精益求精、人力解放、生產(chǎn)效率大幅提高。
11月4日,馬斯克現(xiàn)身2022年度巴倫投資大會(huì),提到一個(gè)工廠小事。他在生產(chǎn)線發(fā)現(xiàn)電池組頂部有三個(gè)玻璃纖維墊,問(wèn)有什么用處?靜音團(tuán)隊(duì)以為那是安全團(tuán)隊(duì)要的,用來(lái)防止火災(zāi);安全團(tuán)隊(duì)以為是靜音團(tuán)隊(duì)要的,用來(lái)降噪。這個(gè)烏龍導(dǎo)致生產(chǎn)線阻塞,馬斯克明白后立馬去掉了玻璃纖維墊。
特斯拉超級(jí)工廠無(wú)疑是當(dāng)今智能工廠的代表。這一細(xì)節(jié)表明,無(wú)論工廠自動(dòng)化、智能化程度多么高,具有自主判斷能力的人,仍然不可或缺。
中國(guó)近幾十年來(lái),有“世界工廠”之稱(chēng),在向智能制造進(jìn)化的途中,如何實(shí)現(xiàn)工廠、機(jī)器、人工智能與人的有機(jī)協(xié)作,共同進(jìn)化,或許是擺在中國(guó)智能制造面前必須要克服的課題。
而這同時(shí)也蘊(yùn)含著刷新中國(guó)智能制造的新內(nèi)涵。
告別狂野增長(zhǎng)
對(duì)于這一問(wèn)題的理解,可以以大規(guī)模手機(jī)生產(chǎn)為例。以前功能機(jī)本身不智能,2007年才開(kāi)始智能,在這之后的10年,智能手機(jī)行業(yè)野蠻生長(zhǎng),機(jī)遇多于挑戰(zhàn)。
作為傳統(tǒng)國(guó)產(chǎn)品牌,OPPO擁有自己的工廠,公開(kāi)資料顯示,與業(yè)內(nèi)其它手機(jī)廠商不同,其手機(jī)自產(chǎn)率超過(guò)80%。
據(jù)OPPO制造與品質(zhì)事業(yè)部總裁郭小聰回憶,OPPO 2008年時(shí)一個(gè)月只能生產(chǎn)20萬(wàn)臺(tái)手機(jī),到2016年增至200萬(wàn)臺(tái)/月,2019年更達(dá)到了2000萬(wàn)臺(tái)/月,十年內(nèi)產(chǎn)能增大了100倍。
這一過(guò)程中,OPPO既要擴(kuò)大自有制造的產(chǎn)能,又要實(shí)現(xiàn)數(shù)字化轉(zhuǎn)型,讓工廠更智能。
然而 ,2017年,全球智能手機(jī)出貨量沖上巔峰,行業(yè)進(jìn)入飽和期,上下游發(fā)生了變化。一方面,消費(fèi)者需求日益精細(xì)化,導(dǎo)致手機(jī)SKU增加;另一方面,廠商的產(chǎn)品品類(lèi)橫向增長(zhǎng),擴(kuò)展至智能手表等IoT產(chǎn)品。OPPO以往一年只生產(chǎn)10-20款產(chǎn)品,現(xiàn)在一年已增至60-80款產(chǎn)品。各方的變化對(duì)制造水平提出了更高的要求。
手機(jī)作為消費(fèi)電子產(chǎn)品頭號(hào)品類(lèi),制造卻不如白電行業(yè)成熟。其特點(diǎn)是市場(chǎng)變化快、產(chǎn)品周期短。需求改變導(dǎo)致生產(chǎn)變化,生產(chǎn)變化意味著產(chǎn)能發(fā)生改變,而產(chǎn)能又會(huì)影響到物流倉(cāng)儲(chǔ);產(chǎn)品生產(chǎn)從定義、測(cè)試到組裝等環(huán)節(jié),標(biāo)準(zhǔn)都不同,例如折疊屏和直板手機(jī)工藝不同,所需要的螺絲標(biāo)準(zhǔn)也不一樣。整個(gè)鏈條若沒(méi)有統(tǒng)一標(biāo)準(zhǔn)管理,將產(chǎn)生大量的資源浪費(fèi),成本增倍。
上世紀(jì)初,福特汽車(chē)用流水線生產(chǎn)模式打開(kāi)了汽車(chē)工業(yè)革命的大門(mén)。這家公司通過(guò)減少SKU,擴(kuò)大規(guī);(yīng),以降低成本,交付更多汽車(chē),讓消費(fèi)者用更低的價(jià)格買(mǎi)到產(chǎn)品。
時(shí)過(guò)境遷,單純調(diào)整生產(chǎn)線已經(jīng)無(wú)法滿足當(dāng)前市場(chǎng)需求,智能化轉(zhuǎn)型才是最優(yōu)解。
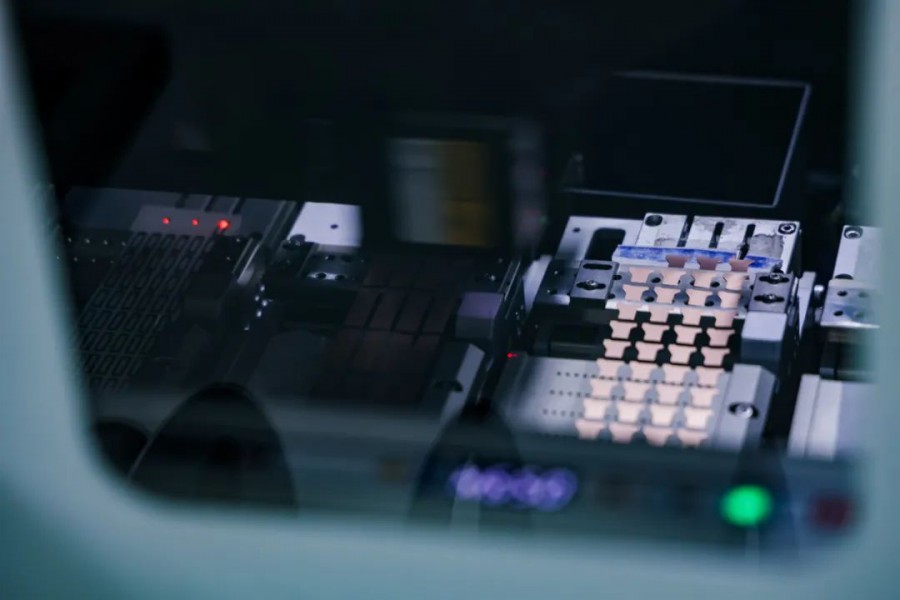
加之市場(chǎng)飽和期,疫情以及國(guó)際經(jīng)濟(jì)形勢(shì)等方面的影響,都證明了原先預(yù)測(cè)訂單生產(chǎn)模式已不適應(yīng)當(dāng)下市場(chǎng)環(huán)境。
調(diào)整已成必然。通過(guò)一系列內(nèi)外疏通,從標(biāo)準(zhǔn)化、自動(dòng)化、數(shù)字化,到智能化,3年時(shí)間,OPPO郭小聰表示,把制造周期從16天調(diào)整到6.8天,最新推出的Reno9即是如此。
他表示,從2023年起,將從預(yù)測(cè)生產(chǎn)模式轉(zhuǎn)為ATO(按訂單式)模式,即不再采用主觀決策,而是先獲取代理商需求,規(guī)范其對(duì)自身訂單的預(yù)估,從而縮短后續(xù)制造流程的時(shí)間。從準(zhǔn)備原料、組裝貼片,到總裝、測(cè)試,再到物流,制造周期進(jìn)一步縮短至6天以下。
機(jī)械臂不等于智能制造
沒(méi)有統(tǒng)一標(biāo)準(zhǔn)前,一切“智能”都是紙老虎。
從2016年到2020年,OPPO內(nèi)部引入了大量的自動(dòng)化設(shè)備,而這些設(shè)備的導(dǎo)入時(shí)間前后差異導(dǎo)致設(shè)備設(shè)計(jì)差異比較大。想要讓所有的設(shè)備保持生產(chǎn)一致性,首先第一步要做的就是標(biāo)準(zhǔn)化。
據(jù)郭小聰透露,公司在2020-2022年期間基本按下了擴(kuò)張“暫停鍵”,不再大量引進(jìn)新設(shè)備,為的是重新梳理工廠里標(biāo)準(zhǔn)化流程。
OPPO 做了三件事情:
第一,物理標(biāo)準(zhǔn)化。彼時(shí)OPPO有15000臺(tái)設(shè)備,要把同功能的不同設(shè)備歸類(lèi),把不同供應(yīng)商設(shè)備歸類(lèi);
第二,數(shù)字標(biāo)準(zhǔn)化。由于不同供應(yīng)商設(shè)備之間的系統(tǒng)完全不同,OPPO花了大量精力搭建新的軟件控制平臺(tái),從而實(shí)現(xiàn)一個(gè)軟件管理不同供應(yīng)商的硬件設(shè)備;
第三,海外建廠標(biāo)準(zhǔn)化。由于國(guó)內(nèi)外的法律法規(guī)等因素,廠房落地的情況不同,OPPO將海外建廠的流程標(biāo)準(zhǔn)化,可實(shí)現(xiàn)全球各地應(yīng)要求快速建廠。
原先中國(guó)企業(yè)數(shù)字化最為人詬病的,就是沒(méi)有自己的軟件系統(tǒng),硬件買(mǎi)回來(lái)能裝,卻需要供應(yīng)商來(lái)管理,這大大影響了生產(chǎn)效率和設(shè)備維護(hù)成本。
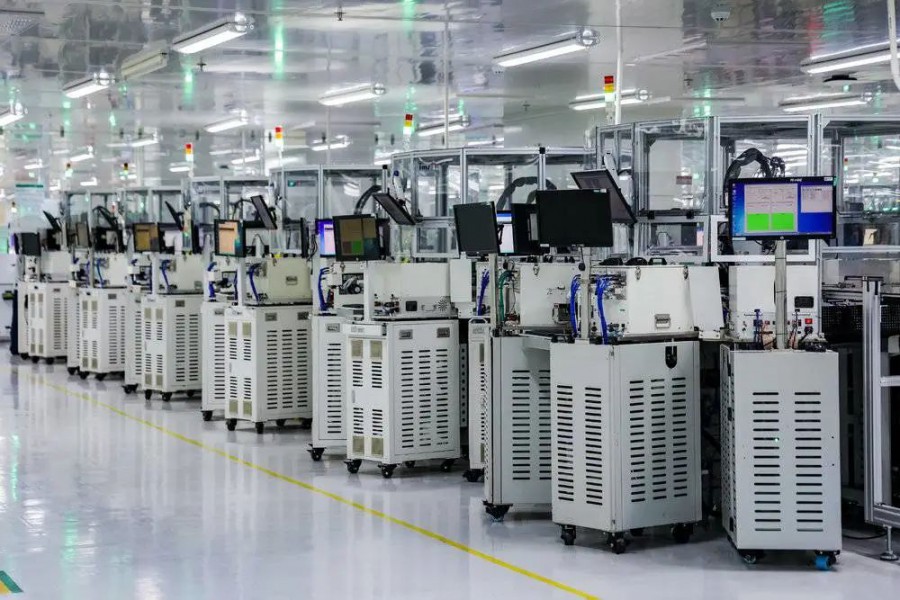
不僅是硬件設(shè)備的軟件不同,財(cái)務(wù)和研發(fā)管理等系統(tǒng)軟件也不同。各系統(tǒng)之間的割裂導(dǎo)致信息不流通,這也是傳統(tǒng)企業(yè)數(shù)字化時(shí)頭疼的問(wèn)題。例如ERP(企業(yè)資源管理)、CRM(全單銷(xiāo)售管理)和TMS(物流運(yùn)輸管理系統(tǒng))之間無(wú)法無(wú)縫交換信息,從上至下的影響,致使管理過(guò)程不透明。
據(jù)郭小聰舉例說(shuō),公司以前與供應(yīng)商的溝通方式比較傳統(tǒng),生產(chǎn)計(jì)劃鏈條一致性很差。外部的訂單需求是一個(gè)計(jì)劃,來(lái)到集成產(chǎn)品交付部,得消化分解成物料需求計(jì)劃和生產(chǎn)執(zhí)行計(jì)劃,供應(yīng)鏈接到的又是新計(jì)劃。一個(gè)鏈條里計(jì)劃混亂,信息無(wú)法打通,溝通成本高。
于是OPPO在2020年啟動(dòng)了供應(yīng)鏈系統(tǒng)變革,以解決內(nèi)部計(jì)劃和外部供應(yīng)商計(jì)劃不一致,完成供應(yīng)鏈管理系統(tǒng)(SRM)升級(jí),打通了跟供應(yīng)商的交付信息鏈路。
到2021年將全公司切換至全新協(xié)同辦公平臺(tái)TT和公司應(yīng)用協(xié)同辦公平臺(tái)MO,把 ERP、PLM、研發(fā)管理和財(cái)務(wù)管理等系統(tǒng)要素集成,用一個(gè)系統(tǒng)串聯(lián)起不同的環(huán)節(jié),讓信息流在同一個(gè)平臺(tái)上跑了起來(lái)。
這些所有前置性的標(biāo)準(zhǔn)定下之后,才算搭建好智能制造基礎(chǔ)。
數(shù)字化轉(zhuǎn)型轉(zhuǎn)到哪里
標(biāo)準(zhǔn)化之后,切實(shí)的自動(dòng)化才能進(jìn)一步實(shí)現(xiàn)“智能”。
Counterpoint Research的數(shù)據(jù)顯示,2021年,中國(guó)貢獻(xiàn)了全球67%的手機(jī)產(chǎn)量,全球每3臺(tái)手機(jī),有2部是中國(guó)造。盡管中國(guó)是全球公認(rèn)的世界工廠,但全球建廠可以降低成本,這又帶來(lái)了新的挑戰(zhàn)。
OPPO全球擁有10個(gè)智能制造中心,包括印度、巴基斯坦和埃及等海外工廠。怎么讓這些工廠標(biāo)準(zhǔn)統(tǒng)一?
首先,在生產(chǎn)環(huán)節(jié)中,OPPO使用了一些技術(shù)手段,實(shí)現(xiàn)了各工廠要求的標(biāo)準(zhǔn)化,通過(guò)(AOI:Auto Optical Inspection)光學(xué)檢測(cè)系統(tǒng)的導(dǎo)入,把對(duì)關(guān)鍵工藝的外觀標(biāo)準(zhǔn)進(jìn)行了量化固化。如在貼片工序之后的印刷流程,通過(guò)全球統(tǒng)一的視覺(jué)檢測(cè)設(shè)備導(dǎo)入,保證了全球各工廠工藝參數(shù)和管控要求的一致,以保證印刷質(zhì)量。
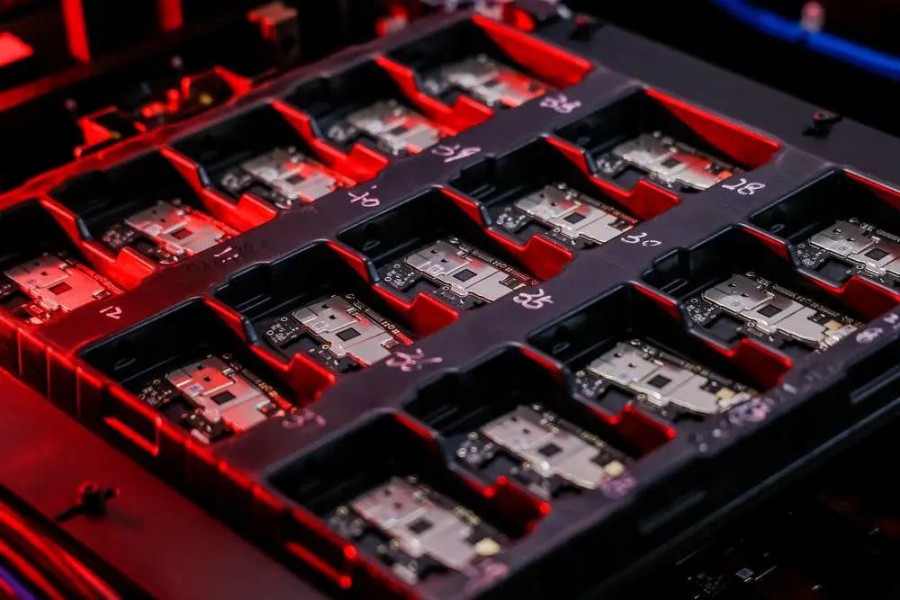
這一環(huán)節(jié)不僅在技術(shù)上代替了肉眼判斷,更精確,且通過(guò)數(shù)字化將判定標(biāo)準(zhǔn)上傳至系統(tǒng),再應(yīng)用到全球其它工廠,可保證各工廠的交付一致性。
其次,OPPO還嘗試了VR方案。如折疊屏手機(jī)的生產(chǎn)涉及新設(shè)備操作與工藝要求,當(dāng)印度工廠需設(shè)備調(diào)試時(shí),工程師就得出國(guó)。OPPO選擇與工業(yè)VR公司合作,通過(guò)遠(yuǎn)程設(shè)備進(jìn)行指導(dǎo)校準(zhǔn),以擺脫國(guó)際人員來(lái)往的束縛。
OPPO不僅自產(chǎn)率超過(guò)80%,還有擁有極強(qiáng)的產(chǎn)業(yè)協(xié)同能力。在數(shù)字化轉(zhuǎn)型過(guò)程中,該能力的優(yōu)勢(shì)被放大。
通過(guò)制造與研發(fā)相互磨合,OPPO優(yōu)化了制造工藝,實(shí)現(xiàn)量產(chǎn)的易制造性、可制造性和可靠性。旗艦產(chǎn)品往往會(huì)使用新材料、新工藝和新設(shè)備,初期生產(chǎn)良率低。通過(guò)產(chǎn)研協(xié)同,設(shè)計(jì)研發(fā)階段就可提前為后續(xù)生產(chǎn)和制造預(yù)留合理公差,避免來(lái)回返工。
郭小聰舉了個(gè)例子,折疊屏講究縫隙控制得好,并保證設(shè)計(jì)方案能讓供應(yīng)商生產(chǎn)出來(lái)。工業(yè)領(lǐng)域,每個(gè)零部件尺寸都在0.01mm上下波動(dòng),而多個(gè)部件疊加會(huì)影響最終的縫隙。在產(chǎn)研協(xié)同幫助下,OPPO折疊屏生產(chǎn)良率行業(yè)居前。
2017年至今,OPPO在設(shè)備領(lǐng)域投入,除了產(chǎn)能擴(kuò)張的設(shè)備,剩下50~60%的設(shè)備投入都用于品質(zhì)提升與標(biāo)準(zhǔn)化、數(shù)字化和智能化升級(jí),總投入接近20億元人民幣。
2020年,OPPO啟動(dòng)了“鳳凰計(jì)劃”,實(shí)現(xiàn)全面數(shù)字化轉(zhuǎn)型。
人性化底色,讓00后參與智能化
在中國(guó)人口眾多、中老年人慢慢增多的人口結(jié)構(gòu)下,拋開(kāi)“人”談數(shù)字化、智能化轉(zhuǎn)型,不切實(shí)際。
此前OPPO重慶工廠里有一個(gè)崗位離職率非常高,每個(gè)月該崗位平均換掉兩個(gè)人。公司做了一個(gè)調(diào)研報(bào)告,發(fā)現(xiàn)“最不愿意干的崗位”排名第一的永遠(yuǎn)是那個(gè)崗位。
調(diào)查發(fā)現(xiàn),原來(lái)該崗位工作強(qiáng)度很強(qiáng),要用手去扣電池蓋。在設(shè)計(jì)中,卡扣越多越牢固,但卡扣越多,員工的手越難受。OPPO發(fā)現(xiàn)問(wèn)題后,馬上找工程師做了一套自動(dòng)化設(shè)備,員工只需做一個(gè)預(yù)扣的動(dòng)作,剩下的裝配步驟便可交給設(shè)備。
如此一來(lái),員工工作強(qiáng)度變小了,該崗位的離職率大大降低。配套措施調(diào)整后,重慶工廠的離職率也從原先15%降低到了2%。
“工人很多反對(duì)自動(dòng)化、智能化,因?yàn)檫@是革他們的工作飯碗。”郭小聰說(shuō)。他對(duì)于數(shù)字化、智能化的定義,是希望未來(lái)所有的工人都能通過(guò)簡(jiǎn)單、低代碼方案提升自己工作效率。
以人為本,是OPPO數(shù)字化轉(zhuǎn)型核心。OPPO的POU手邊化(衡量工人不用挪動(dòng)身體作業(yè)的一個(gè)指標(biāo))達(dá)到了90%,員工不需要轉(zhuǎn)身、彎腰和走動(dòng),就能完成他觸手可及半徑內(nèi)的所有作業(yè)。OPPO還推出了五星人才激勵(lì)計(jì)劃,建立員工晉升通道,可從技能成長(zhǎng)到薪酬福利等方面得到支持。
越來(lái)越多的00后進(jìn)工廠,相比之下,他們更加厭倦傳統(tǒng)的機(jī)械化工作方式。但隨著智能化轉(zhuǎn)型深入,困擾著00后進(jìn)廠的問(wèn)題正在得到解決。
智能化轉(zhuǎn)型的本質(zhì)是為了追求生產(chǎn)效率,而“人”應(yīng)當(dāng)隨著轉(zhuǎn)型升級(jí),由原先的基礎(chǔ)工作升級(jí)為更高質(zhì)量的工作,從而提高員工的產(chǎn)出。郭小聰認(rèn)為智能制造不是自上而下的管理,而是從上面推動(dòng),下面能加入,大家共同達(dá)成全員數(shù)字化、智能化目標(biāo)。
尾聲
全球競(jìng)爭(zhēng)中,中國(guó)制造正在經(jīng)受挑戰(zhàn)。對(duì)于未來(lái)的競(jìng)爭(zhēng),主流意見(jiàn)已經(jīng)明確,發(fā)展實(shí)體經(jīng)濟(jì),走高質(zhì)量路線。
從拼價(jià)格,到拼品質(zhì),中國(guó)智能制造轉(zhuǎn)型升級(jí),最核心變量,依然是人。
早在2013年,德國(guó)就提出工業(yè)4.0的概念,美國(guó)也正在重新憧憬實(shí)體制造榮光。中國(guó)擁有全球最大的一塊工業(yè)沃土,產(chǎn)業(yè)鏈?zhǔn)滞暾,從上游材料再到下游組裝,這里可以形成一個(gè)完整的手機(jī)產(chǎn)業(yè)鏈閉環(huán),還擁有強(qiáng)大的工業(yè)技術(shù)保障和人才體系保障。在現(xiàn)有優(yōu)勢(shì)上,如何讓人與智能產(chǎn)線和諧相處,共同進(jìn)化,才是未來(lái)中國(guó)實(shí)體經(jīng)濟(jì)制勝之道。
OPPO是業(yè)內(nèi)少有的產(chǎn)研一體科技企業(yè),但目前OPPO已取得了一些階段性成果:SMT自動(dòng)化生產(chǎn)達(dá)到85%,自動(dòng)化測(cè)試達(dá)到90%,SMT 全自動(dòng)生產(chǎn)線和總裝生產(chǎn)效率都處于行業(yè)領(lǐng)先。每條生產(chǎn)線平均每10秒生產(chǎn)一臺(tái)手機(jī),對(duì)比2020年,一臺(tái)機(jī)器制造成本下降接近40%。
智能化轉(zhuǎn)型這條路,播下的是一顆待收獲的種子。
這讓人想到當(dāng)年OPPO堅(jiān)持自身特色的篤定。2012年,互聯(lián)網(wǎng)手機(jī)爆火,外界紛紛認(rèn)為線下渠道會(huì)被電商攻破時(shí),OPPO依舊堅(jiān)持經(jīng)營(yíng)線下渠道精細(xì)化、人性化轉(zhuǎn)型、深耕,終于在2016年爆發(fā),明星機(jī)型R9售出2000萬(wàn)臺(tái),成為安卓機(jī)單品銷(xiāo)量冠軍。
假以時(shí)日,OPPO堅(jiān)持的人性化底色的智能進(jìn)化,或許能成為中國(guó)智能制造轉(zhuǎn)型升級(jí)道路上一道風(fēng)景。